Professional Advice on What is Porosity in Welding and Exactly How to Address It
Professional Advice on What is Porosity in Welding and Exactly How to Address It
Blog Article
The Science Behind Porosity: A Comprehensive Guide for Welders and Fabricators
Recognizing the complex systems behind porosity in welding is important for welders and fabricators pursuing impeccable craftsmanship. As metalworkers explore the midsts of this sensation, they uncover a world governed by various aspects that influence the formation of these minuscule gaps within welds. From the make-up of the base products to the ins and outs of the welding procedure itself, a plethora of variables conspire to either aggravate or alleviate the visibility of porosity. In this comprehensive guide, we will certainly untangle the science behind porosity, exploring its results on weld quality and introduction advanced techniques for its control. Join us on this journey with the microcosm of welding flaws, where precision fulfills understanding in the pursuit of perfect welds.
Comprehending Porosity in Welding
FIRST SENTENCE:
Exam of porosity in welding reveals important understandings into the stability and high quality of the weld joint. Porosity, identified by the existence of dental caries or gaps within the weld metal, is a typical issue in welding procedures. These gaps, if not appropriately addressed, can endanger the structural stability and mechanical buildings of the weld, causing prospective failures in the ended up item.

To spot and evaluate porosity, non-destructive testing approaches such as ultrasonic testing or X-ray examination are often employed. These methods allow for the identification of inner flaws without compromising the honesty of the weld. By examining the dimension, form, and circulation of porosity within a weld, welders can make enlightened choices to enhance their welding processes and achieve sounder weld joints.

Factors Affecting Porosity Formation
The incident of porosity in welding is affected by a myriad of variables, ranging from gas shielding performance to the details of welding specification setups. Welding criteria, consisting of voltage, present, travel rate, and electrode kind, also impact porosity development. The welding strategy employed, such as gas metal arc welding (GMAW) or protected steel arc welding (SMAW), can affect porosity formation due to variants in warm distribution and gas insurance coverage - What is Porosity.
Results of Porosity on Weld High Quality
The existence of porosity additionally deteriorates the weld's resistance to rust, as the entraped air or gases within the spaces can respond with the surrounding atmosphere, leading to deterioration over time. In addition, porosity can prevent the weld's capability to hold up against more info here stress or impact, additional endangering the total high quality and reliability of the bonded framework. In vital applications such as aerospace, automotive, or structural building and constructions, where security and resilience are critical, the damaging results of porosity on weld quality can have serious effects, highlighting the significance of minimizing porosity via correct welding techniques and treatments.
Strategies to Minimize Porosity
To enhance the high quality of welded joints and guarantee structural integrity, welders and fabricators employ details strategies targeted at minimizing the formation of voids and tooth cavities within the product throughout the welding procedure. One efficient technique to lessen porosity is to make certain proper product preparation. This consists of thorough cleaning of the base steel to eliminate any type of pollutants such as oil, grease, or wetness that could contribute to porosity development. Additionally, using the proper welding criteria, such as the proper voltage, present, and travel rate, is crucial in stopping porosity. Maintaining a constant arc learn this here now size and angle throughout welding likewise helps in reducing the likelihood of porosity.

Using the proper welding technique, such as back-stepping or using a weaving movement, can also aid disperse heat evenly and lower the possibilities of porosity formation. By implementing these methods, welders can successfully lessen porosity and produce top notch welded joints.
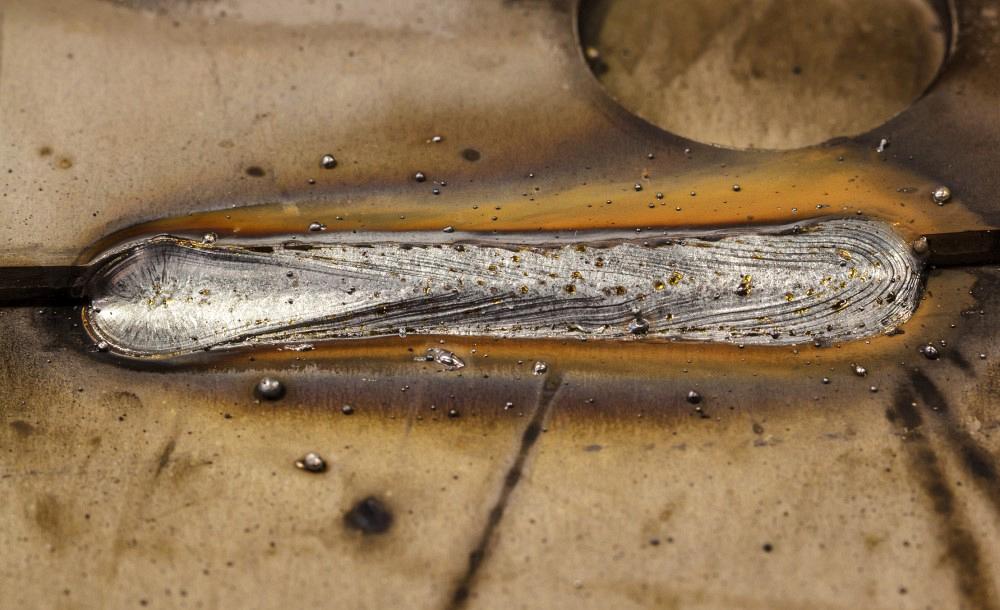
Advanced Solutions for Porosity Control
Carrying out advanced innovations and cutting-edge methods plays a crucial function in accomplishing exceptional control over porosity in welding procedures. One advanced remedy is making use of innovative gas mixes. Shielding gases like helium or a blend of argon and hydrogen can help in reducing porosity by supplying much better arc security and boosted gas protection. In addition, utilizing sophisticated welding methods such as pulsed MIG welding or modified ambience welding can also help mitigate porosity concerns.
An additional advanced option entails using advanced welding devices. Using devices with built-in attributes like waveform control and sophisticated power sources can enhance weld quality and lower porosity threats. In addition, the execution of automated welding systems with accurate control over specifications can substantially reduce porosity issues.
Moreover, including advanced surveillance and examination modern technologies such as real-time X-ray imaging or automated ultrasonic testing can help in spotting porosity early in special info the welding process, permitting instant corrective actions. Overall, integrating these advanced solutions can substantially enhance porosity control and enhance the general quality of bonded elements.
Final Thought
In conclusion, comprehending the science behind porosity in welding is crucial for welders and producers to generate top quality welds - What is Porosity. Advanced remedies for porosity control can further improve the welding procedure and guarantee a solid and trusted weld.
Report this page